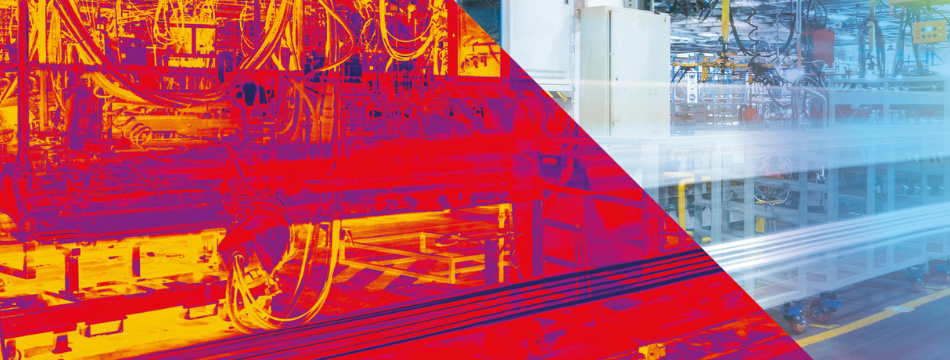
There are a plethora of challenges facing 2025’s manufacturing industry. A widening skills gap and volatile economic landscape pressure manufacturers to produce high-quality goods faster and cheaper, while adopting ever-evolving technological advancements. Consequently, many systems are pushed to their limits, with some running 24/7 to maximise output and meet rising customer expectations. With such slim margins separating success and catastrophe, even the smallest equipment failure can have a devastating impact on production and profit. Moreover, traditional maintenance and monitoring approaches are proving ineffective in the face of today’s high-volume, high-quality, high-pressure production. This is where FLIR’s Manufacturing Advantage can transform your maintenance routine to maximise your output, maximise your profitability, and minimise your stress![1]
Quick Links
- Predictive Maintenance vs Preventive Maintenance
- Reasons for Preventive Maintenance & Predictive Maintenance
- What’s FLIR’s Manufacturing Advantage
- Further Information
Predictive Maintenance vs Preventive Maintenance
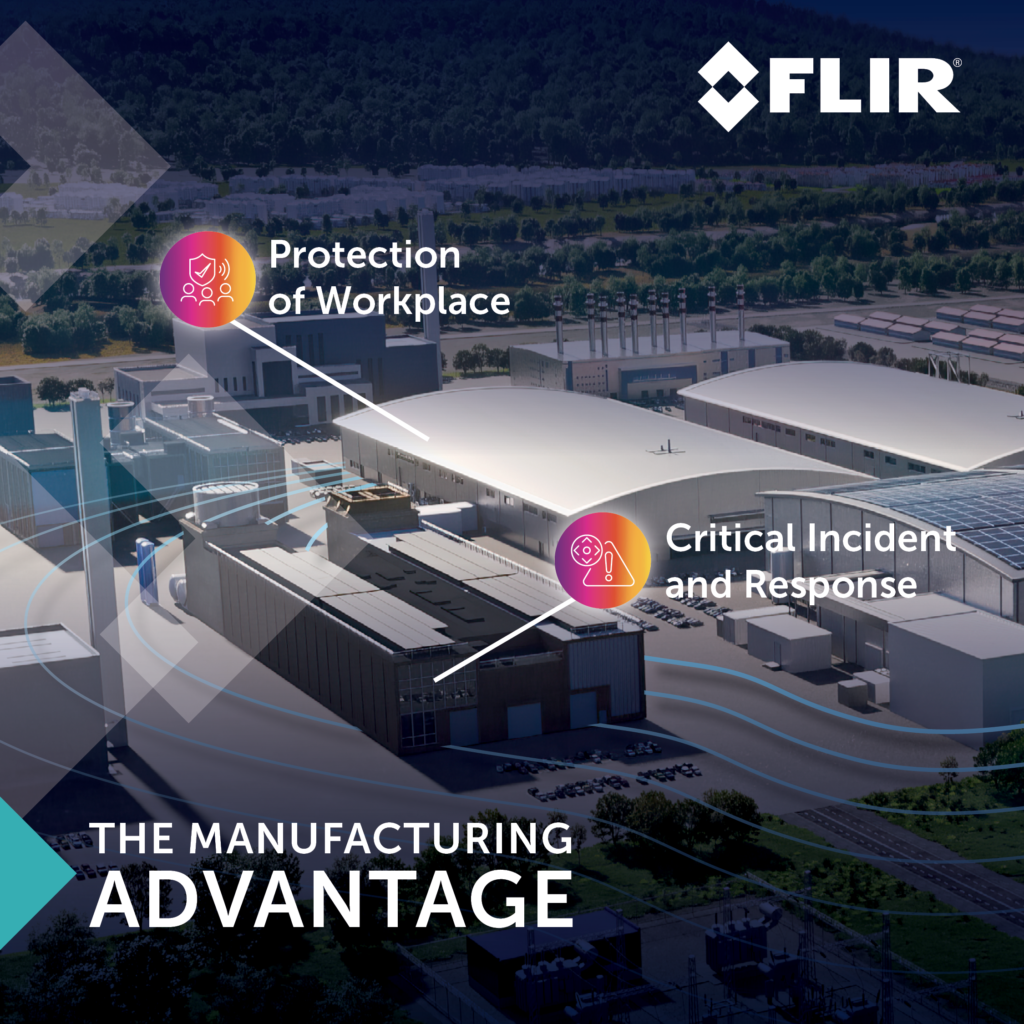
Good manufacturing practices incorporate both predictive and preventive maintenance.[2] In today’s demanding industrial sector, focused on high-output, just-in-time manufacturing, the previous strategy of letting equipment run to failure before addressing issues is no longer viable. It’s too costly, both in terms of repair/replacement and downtime. Excessive downtime significantly reduces production, causing manufacturing plants to miss deadlines and lose profits. Predictive and preventive maintenance offer effective methods of detecting problems early, thereby reducing repair costs and downtime.
Preventive and predictive maintenance are two separate maintenance techniques. Manufacturing plants need to implement both to reap the benefits. So, what is the difference between predictive maintenance and preventive maintenance?
What’s Preventive Maintenance?
Preventive or routine maintenance involves performing regular inspections and/or repairs on equipment at pre-defined intervals. Scheduling maintenance inspections at regular periods enables manufacturing plants to catch issues earlier, consequently reducing unexpected downtime and repair/replacement costs. Breaks between inspections tend to be based on one of the following:
- Usage: intervals are set according to asset use, e.g., replacing a car’s tyres every 50 000 miles.
- Calendar/time: maintenance checks are performed routinely at specific times, for instance, having your boiler checked/serviced annually.
- Condition: factors such as wear and degradation inform maintenance schedules, including inspection intervals.
Preventive maintenance could include equipment and component inspection, calibration, cleaning, repair, and replacement. As such, a manufacturing plant may implement several preventive maintenance routines to be conducted at different times. For example, cleaning may occur every day; equipment and component inspection might happen every week or month; and calibration, repair, and replacement may take place annually or biannually.
Preventive maintenance inspections always go ahead as planned, regardless of whether identifiable issues are present. Additionally, most routine inspections necessitate operational downtime. As a consequence, production must be halted, seemingly jeopardising deadlines and profits. However, unlike reactive/traditional (as outlined above) maintenance, with preventive inspections, downtime is already factored in to the process. As such, halts in production can be planned for less busy periods, minimising the impact on output and profits.
What’s Predictive Maintenance?
Conversely, predictive maintenance or condition monitoring requires no downtime. Using condition monitoring tools, such as thermal cameras and acoustic imagers, often combining them with advanced data analysis tools and/or maintenance management systems, manufacturing plants can assess equipment condition in real-time. Data gathered and analysed with these systems enables teams to conclude whether repairs or replacements are required. Not only does this limit downtime to just that required to make necessary adjustments, but it also allows teams to spot potential problems earlier. As a result, engineers can take corrective action sooner, extending equipment longevity and reducing repair costs.
Nucleus Research reports that:
“Predictive maintenance initiatives reduce downtime by between 30 and 50 percent, extend asset lifespan by between 20 and 40 percent, lower costs, improve safety, and enhance product quality.”[3]
Reasons for Preventive Maintenance & Predictive Maintenance
As outlined, predictive and preventive maintenance decrease downtime, extend equipment longevity, and reduce repair costs. All critical aspects in a modern manufacturing sector that lives and dies on facilities’ ability to balance “operational efficiency and product quality while safeguarding profitability.”[4]
Reflecting on the role of predictive and preventive maintenance within the manufacturing industry, Rob Milner, FLIR’s Director of Business Development for Condition Monitoring and First Responders, stresses that:
“In this environment, condition and quality monitoring is no longer optional – it’s a strategic necessity. Advancements in thermal and acoustic imaging technologies and products allow manufacturers to operate at full capacity while mitigating the risks of equipment failure or quality issues, ensuring they can meet the demand without compromising performance.”[5]
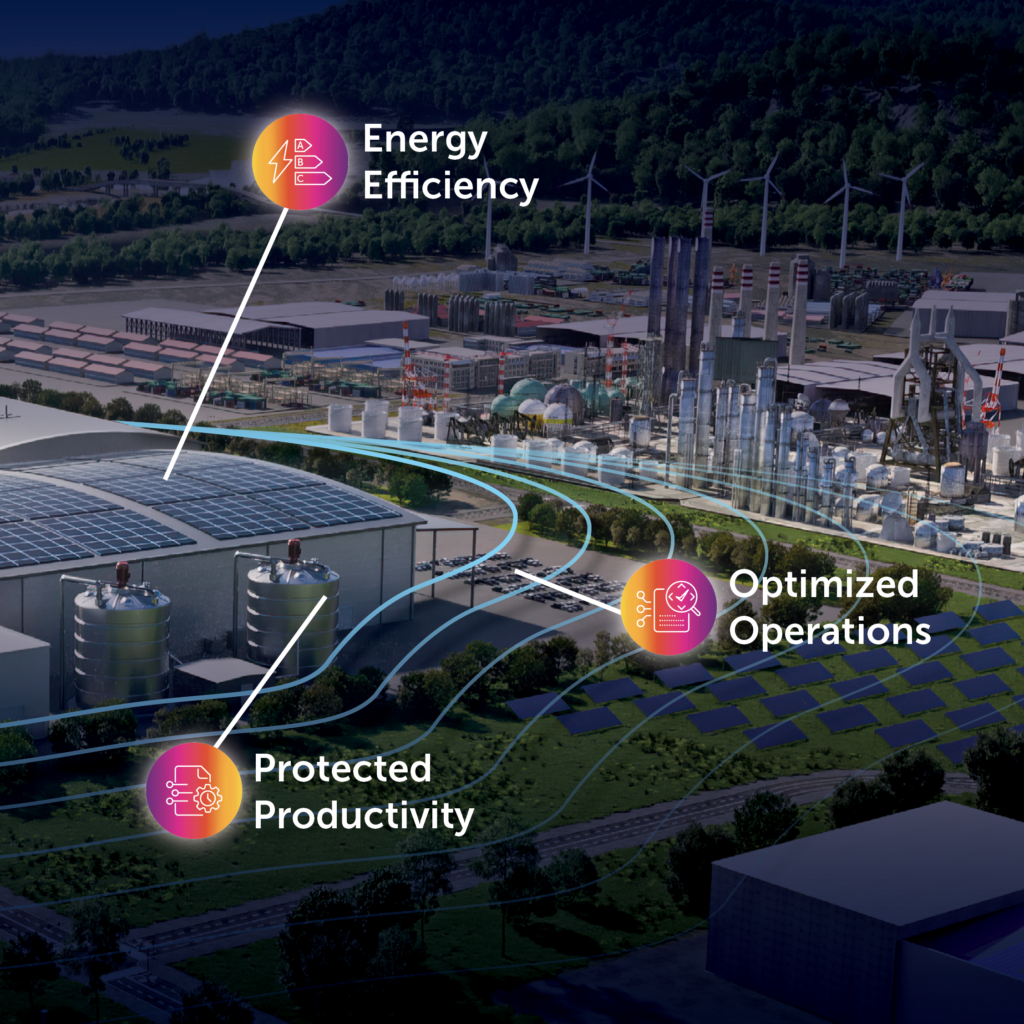
His sentiments are echoed by Jerry Beeney, FLIR’s Director of Business Development for Systems and Programs, who, remarking on the importance of automated condition and quality monitoring tools, says:
“It’s time to stop viewing these products and services as standalone and ‘moment in time’ tools. We know that when you embed monitoring into every aspect of the production process, you not only prevent failures but also unlock new levels of efficiency and quality. It’s the vision to see the bigger picture, through technology and expertise that enables predictive maintenance and real-time quality control. This use of critical data to drive long-term performance helps companies stay ahead of market demands.”[6]
Ultimately, predictive and preventive maintenance will enable factories to keep pace with modern, ‘just-in-time’ manufacturing expectations without compromising product quality and while reducing manufacturing costs; consequently, maximising profitability.
Why Preventive Maintenance is Necessary
- Eliminate unplanned downtime
- Restrict downtime to planned sessions during periods of low productivity
- Spot problems earlier
- Reduce repair/replacement costs
- Improve equipment longevity
- Optimise energy efficiency by ensuring equipment is working correctly
- By reducing downtime, repair/replacement costs, and energy bills, preventive maintenance improves productivity and profitability
Why Predictive Maintenance is Important
- Eliminate unplanned downtime
- Maximises uptime as predictive maintenance tools inspect and gather relevant data during regular operations
- Limit downtime to just repair time
- Maintain high output
- Spot problems earlier
- Reduce repair/replacement costs
- Improve equipment longevity
- Optimise energy efficiency by ensuring equipment is working correctly
- Increased productivity, combined with reduced repair/replacement and energy bills, improves profitability
What’s FLIR’s Manufacturing Advantage?
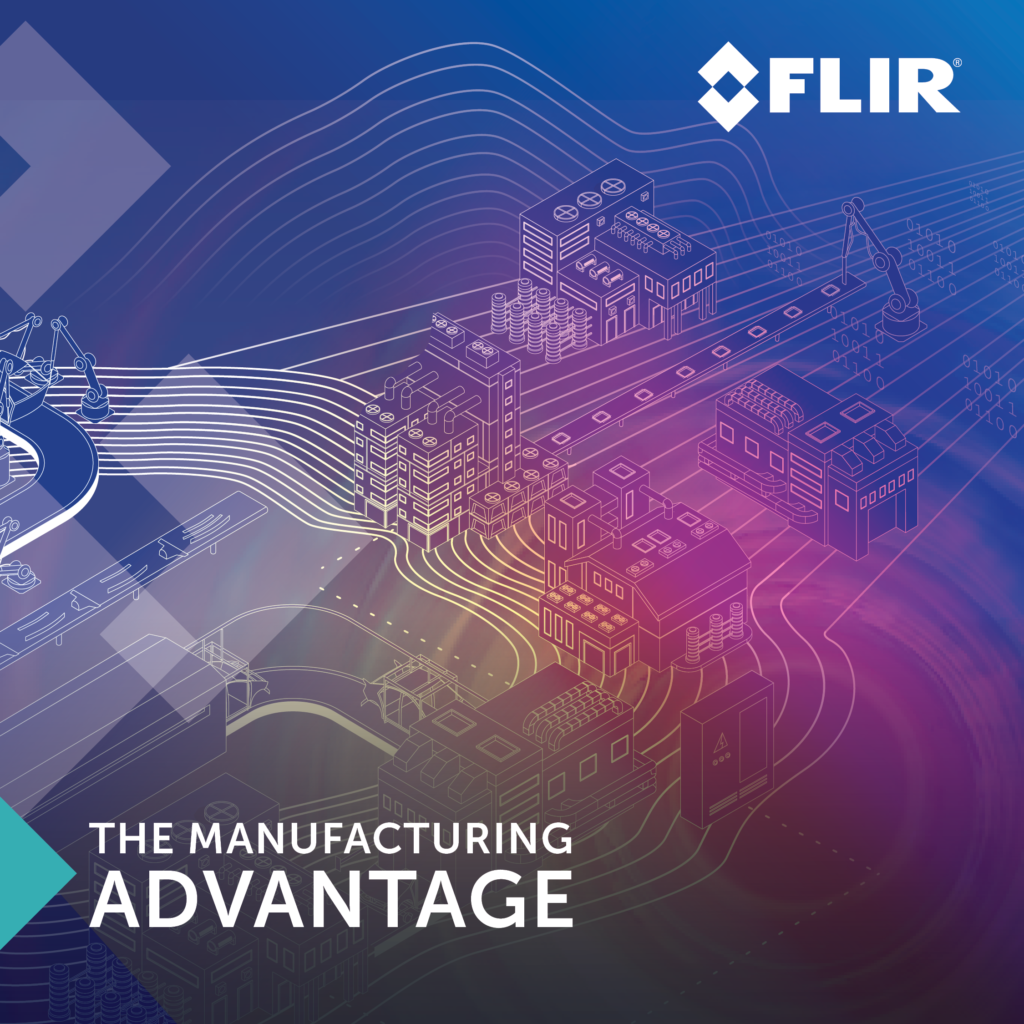
Success in manufacturing often depends on the small details: overheating components, worn cable connectors, or faulty electric motors can be the difference between optimal operation and unscheduled downtime. Moreover, subtle changes in temperature, small vibration alterations, and/or minute leaks may be the key to discovering issues before catastrophic failure. FLIR understands this. For 50 years, FLIR has led the way in developing tools designed to help manufacturing facilities spot potential problems early, improving the “efficiency, safety, security, and competitive positioning”[7] of their businesses.
Shop FLIR Preventive & Predictive Maintenance Tools
FLIR’s innovative outlook, in-depth expertise, and profound knowledge of their customers’ pain points have enabled them to develop industry-leading thermal imaging cameras and advanced monitoring technologies that offer bespoke solutions to a range of challenges. Always looking to the future, FLIR has recently introduced a range of acoustic imaging cameras to its portfolio. These sophisticated yet easy-to-use imagers are specifically designed to empower manufacturing and high voltage maintenance teams to find and address issues, such as partial discharge and compressed air leaks, before they result in plant failure.
Shop FLIR’s Si-Series Acoustic Imagers
In respect to FLIR’s proven success and legacy of innovation, the FLIR manufacturing advantage could be defined as:
“Our [FLIR’s] expertise, experience and technologies delivering the attention to detail that protects your big picture. We [FLIR] have the vision to drive your strategies, enhance operations, and safeguard your assets, your people, and your competitive edge.”[8]
Central to the FLIR ethos is their determination to help businesses fulfil the three Cs: Change, Comparison, and Chronology. Only by addressing the three Cs can companies understand asset health enough to minimise downtime, extend longevity, and optimise operations.
Change
Noticing changes, such as minor temperature increases, can be the difference between spotting and not spotting a problem. To this end, FLIR has developed an eclectic catalogue of handheld and fixed thermal imaging cameras. All are fitted with FLIR’s image processing technologies designed to enhance thermographs by reducing noise and improving contrast. Most FLIR thermal cameras include Multi-Spectral Dynamic Imaging (MSX®), which overlays visual imagery onto a thermograph in real-time. Consequently, maintenance engineers are provided with a detailed, combined digital and thermal picture, making it easier to pinpoint the source of anomalous temperatures.
Some FLIR thermal cameras complement MSX imaging with UltraMax® imaging. This feature captures multiple thermal images in rapid succession and combines them to create a single detailed, higher-resolution image. More pixels also means more temperature data, as each pixel contains a unique reading. Once again, this makes noticing temperature changes simpler and more accurate.
Similarly, compressed air leaks and partial discharge (PD) can also be indicative of emerging faults and/or excess energy consumption, both costly. In these situations, FLIR’s intelligent acoustic imagers come into their own. Equipped with algorithms for leak quantification and PD assessment, FLIR’s Si Acoustic Imagers allow maintenance teams to find and evaluate potential problems in real time, ensuring maintenance plants can make informed data-backed repair decisions. Moreover, these algorithms can be used to quantify savings, allowing you to compare faults before and after corrective action, thereby assessing the effectiveness of repairs.
Comparison
Establishing a benchmark for equipment is critical to understanding whether there has been a change in operation. For meaningful comparisons, data must be gathered under repeatable conditions. For instance, equipment should be operating under the same load and thermal or acoustic data ought to be collected from the same point. To help with this, many of FLIR’s thermal imaging cameras support Route Creator Technology. Using this software, teams can create customised inspection paths that may be uploaded to a compatible FLIR thermal camera. This ensures that data will be gathered in the correct order and at the same point, regardless of which team member is charged with conducting the inspection.
Alternatively, FLIR’s A-series Automation Thermal Cameras may be mounted to monitor specific equipment, feeding information into a video management system that allows teams to compare data from multiple cameras. Consequently, maintenance engineers can spot outliers quickly: that is, equipment operating at a temperature higher or lower than other pieces of the same equipment. Additionally, FLIR’s automation thermal cameras may be configured to send an alert when equipment breaches a pre-defined temperature range. This ensures potential problems are not missed and empowers teams to deal with impending issues quickly.
Chronology
Another advantage of fixed automated thermal imaging is that it enables continuous 24/7 monitoring. Teams can track temperatures in real-time, allowing them to establish trends and, therefore, predict potential problems. As such, maintenance teams are able to address faults before they materialise, potentially eliminating downtime and significantly reducing repair costs, while improving energy efficiency.
It is also possible to track and trend equipment health using handheld thermal imagers and/or acoustic imagers, provided inspections are conducted at regular intervals (e.g., quarterly, biannually, or annually) and data is captured under comparable conditions. FLIR’s analysis and reporting software, Thermal Studio Pro, may be used to organise, analyse, and trend data, as well as create reports.
Further Information
For more information about how you can leverage FLIR’s manufacturing advantage, contact our Sales team on 01642 931329 or via our online form.
Alternatively, to learn more about how FLIR’s tools could improve operations at your facility, please consult our case studies and articles on this subject.
- Thermal Imaging: The Key to Data Centre Maintenance
- FLIR Automation Thermal Cameras Revolutionise Recycling Centre Fire Prevention
- FLIR A-Series Automation Thermal Cameras Case Study: Electrical & Mechanical Installations
- Conquering Compressed Air Leaks: Seeing Sound & Saving Money with FLIR’s Si-Series Acoustic Cameras
- FLIR Si124 Acoustic Imager Improves Productivity at Pharmaceutical Plant
- FLIR Si124 Acoustic Imager Application Scenario: Condition Monitoring in Pulp & Paper Mills
In the meantime, you can browse our eclectic range of FLIR tools, including thermal cameras and acoustic imagers, at tester.co.uk
[1]Information for this blog has been gathered from the following sources:
- FLIR, FLIR: Defining the Advantage, last accessed 20 May 2025.
- FLIR, FLIR Manufacturing Advantage, last accessed 20 May 2025.
- FLIR, Thermal Imaging in Critical Asset Health Monitoring: The Details That Deliver Advantage, last accessed 20 May 2025.
- FLIR, Unlock the Manufacturing Advantage, last accessed 20 May 2025.
- FLIR, Work Smarter with FLIR: The Manufacturing Advantage, last accessed 20 May 2025.
Additional references in subsequent footnotes.
[2] Information for this section was gathered from the following sources:
- Chris DeBrew, ‘Difference Between Preventive vs. Predictive Maintenance’, ATS, last accessed 20 May 2025.
- Fluke, Preventive maintenance vs predictive maintenance vs proactive maintenance, last accessed 20 May 2025.
- Lynda Gulvin, ‘Preventive maintenance vs. predictive maintenance’, IBM, last accessed 20 May 2025.
[3] Nucleus Research, Quantifying the value of predictive maintenance, last accessed 20 May 2025.
[4] FLIR, Unlock the Manufacturing Advantage.
[5] FLIR, Unlock the Manufacturing Advantage.
[6] FLIR, Unlock the Manufacturing Advantage.
[7] FLIR, FLIR: Defining the Advantage.